Flex PCB Assembly: The Key To Lightweight And Durable Electronics
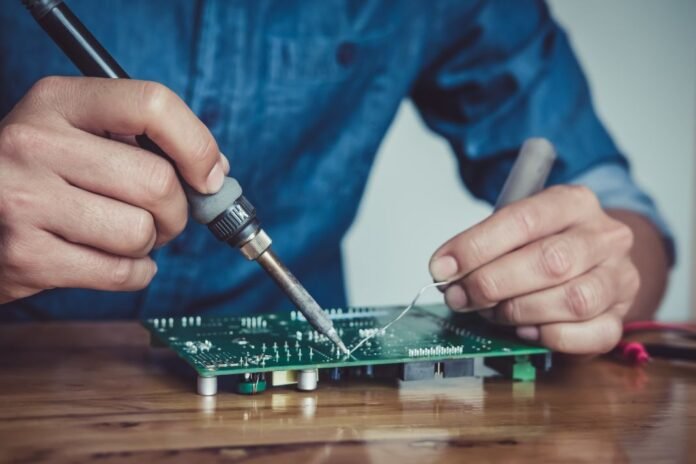
Consumers buying their next phone will typically check the specs sheet to compare their options according to sleekness, price, processing speed, storage and battery life. For products like smartwatches, the same specifications are also important along with connectivity, sensor capability and display type.
These popular and useful electronic devices consist of thousands of hardly seen internal components mounted on Printed Circuit Boards or PCBs. With the increasing need for miniaturized electronics, PCBs are also continuously challenged to be designed and produced as small as possible. In addition to coping with this demand, flexible substrates PCB have been developed that are tailored to applications where space and dimensions need to be restricted.
This blog article will help us gain a better understanding of flex PCB assembly and its significant role in lightweight and durable electronics.
What Is Flex PCB Assembly?
Flex PCB assembly refers to the method of placing components on a thin flexible PCB substrate using Surface Mount Technology or SMT. The flexible substrate is made from a flexible polymeric tape or film that is laminated into a conductive layer. Despite its thin configuration, the flexible base is a high-temperature and high-strength type of polymer material.
Flex PCB can be found in many applications such as consumer electronic products, medical applications and automotive devices. The flexibility of this type of printed circuit board allows free movement and twisting or bending of parts such as in printer heads and in flat panel displays. Despite minimal space and tight turns, flex PCBs can conform well to various geometries.
Just like rigid PCBs, flex circuit board assembly follows almost similar processing steps as below:
Solder Paste Printing
The flex PCBs are secured on rigid carrier jigs to allow automated processing in the SMT (Surface Mount Technology) line. Solder paste printing is carried out using a stencil printing machine.
Component Pick And Place
Component placement is done using a high-speed automated Pick-and-Place machine. Using a vision system, the machine can accurately position the components with some tolerances.
Reflow Soldering
The solder paste is melted and cured in a convective oven using a defined temperature profile. Many factors during reflow soldering can affect the quality of metallurgical joints such as unoptimized time and temperature and even unstable flex PCBs that can result in movement during reflow.
Automated Optical Inspection (AOI)
Automated Optical Inspection or AOI is an essential process in verifying the acceptability of the assembled flex PCBs. The accuracy of inspection is often influenced by resolution and lighting. The settings need to be optimized as the instability and the shining surface of the thin flex can cause some distortion on the captured AOI images.
X-ray Inspection
As there are constraints with AOI due to its limited line-of-sight, x-ray imaging is required to capture images of the solder sitting beneath the components. This is important, especially for crucial active components where complete attachment should be ensured with the controlled presence of voids or air gaps.
Testing
Flex PCBs are electrically tested to check for functionality of the components and overall PCB. The test equipment is made of a test fixture with probes to check the electrical connections of the circuitry.
What Are The Applications Of Flex PCB Assembly?
The direction going to smaller and faster devices has driven further production of flex PCB in the PCB market. Flex PCB assembly production can affect the many sophisticated applications quality so it is important to control the assembly quality.
Consumer Electronics
Consumer electronics is the most visible application in which flexible circuits are heavily utilized. Modern smartphones and laptops have significantly reduced in size due to the shrinking of board sizes and the conversion of some of their rigid parts to flexible sections. Smartwatches and other wearables are also very convenient to use, thanks to the development of flex PCBs that are thin enough to fit into these modern-looking gadgets.
Automotive
Driving cars nowadays have upgraded due to more enhanced features such as infotainment, automated braking systems, lane assistance and many more. Parts such as Engine Control Units or ECUs, sensors, and lighting systems are integrated with flexible circuit boards for smaller form factor electronics.
Medical Devices
Healthcare apparatus and monitoring devices also consist of flex PCBs as these devices should practically be able to conform to body surfaces. The conditions of in-care patients can be remotely tracked with the help of these flexible technologies. Diagnostic instruments such as heartbeat monitoring, MRI and CT imaging scanners employ flex PCBs due to their versatility and reliability.
What Are The Benefits Of Flex PCB Assembly In Lightweight And Durable Electronics?
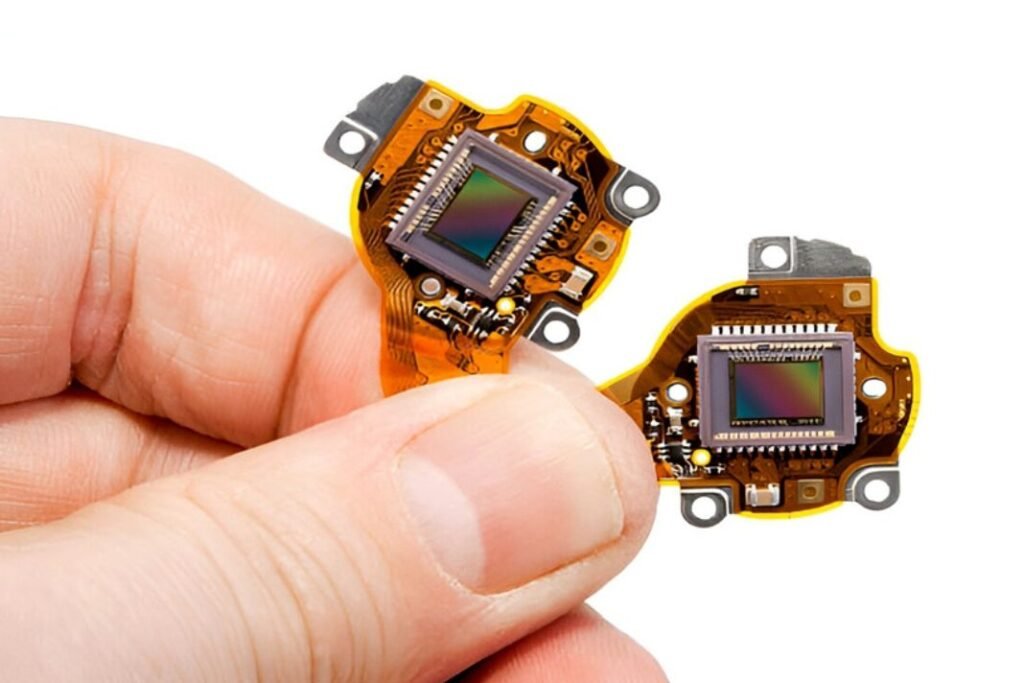
The flex PCB technology is well-known, especially in wearable devices where the requirement focuses on thin and lightweight materials for user-friendliness. Due to its sophisticated application in some portable devices flex PCB assembly quality control is relatively higher. PCB assembly in China enables the production of PCBs to meet various characteristics. Below are the main motivations why flex PCB has a vast range of essential applications.
Flexibility
The most commercially used flex PCBs are polyester and polyimide films. These PCB materials exhibit good flexibility which can fit many geometric configurations. Flex PCBs can adapt to irregularly shaped surfaces as they can be folded, bent, twisted and rolled. These unique capabilities allow flex PCBs to achieve requirements for small devices that have space limitations.
Mechanical Strength
Flex PCBs have high mechanical strength, with the ability to resist fracturing even when fabricated in rolls or blanks. They have good dimensional stability even with high moisture absorption in humid conditions and even with high temperatures.
Lightweight
Weight reduction is one of the key benefits of flexible circuits. This is the primary reason why it is a top choice for wearable electronics. Flex PCB allows smaller form factor and lightweight design that are also integral for other applications such as medical and consumer electronics.
Cost Effectiveness
With flex printed circuit boards, the overall cost may be reduced by eliminating the need for multiple cables and bulky wirings. Being able to remove complex wirings also simplifies the electronics assembly process. Flex PCBs also well adapt to large-scale manufacturing due to their favorability to panelized processing.
Also Know About: Top 5 Challenges In HDI PCB Design